How to choose the right rotor for your rotary valve?
09/03/2022What goes into a rotor, comes around in the rotor, and—if you’ve picked the right one for your application—it produces maximum output.
There are a few rotors to choose from, and not all of them will treat your material the way it needs to be treated. Here’s our breakdown of each kind of rotor and how it works, to give you a better idea of what could work best for your application.
Closed End Rotor
A closed end rotor has a disc attached to the rotor blades, ultimately preventing the blades from touching the endplates. There is a gap between the disc and the endplates that allows any material that does end up outside of the rotor to fall out the bottom easily.
Closed end rotors are used with extremely abrasive material, and flake or chip material as the shield protects the outboard bearings and endplates from damage. It also prevents material from building up on the endplates, causing wear.
Open End Rotor
Compared to closed end, open end rotors are generally easier to clean and maintain, which could ultimately lead to less material build up and wear on your valve. They are also better suited to mechanical seal applications. This is also a better option with lighter materials, as closed end rotors are more likely to have materials escape into the space between the endplates and the rotor disc.
Metering Rotor
Metering rotors are small precision rotors for extremely controlled flow. They are used when smaller amounts or test batches of material are needed.
Staggered Pocket Rotor
Staggered pocket rotors have 16 offset pockets. They are recommended where more uniform flow is needed. With regular rotors, there are short breaks between when the material moves through the system as the rotor moves on its axis. Staggered pocket rotors allow for a continuous and smooth movement of the material into the system.
Reduced Volume Rotor
Another type of metering rotor, reduced volume rotors reduce the Cubic Foot per Revolution (CFR) inside the valve. If a system has too much material moving into it, or the material flows too easily through the system, it could choke up the line beyond the valve. With reduced CFR, it’s easier to control the flow.
Helical Rotor
The helical rotor is meant to act as a knife if any material gets caught between the rotor and the housing, to prevent any jams in the valve. Generally used for wood chips, if the material is going to get stuck, the rotor will cut it and continue to move.
Adjustable Rotor
With very harsh and abrasive material, tips will wear prematurely. With this type of valve, you can adjust the tips by sliding them up as they wear to keep them compliant and keep the clearance as close to their starting point as possible. This ultimately helps your valves last longer.
Flex Tip Style Rotor
There are a few different types of flex tip rotors, depending on what material you’re working with. The purpose of this type of rotor is to prevent material jams inside the valve. Unlike the helical rotor, which slices the jammed material, the flex tips can bend out of the way while moving the material through the valve and keeping a tight seal.
Radius Pocket
This rotor’s pockets are U-shaped. The pocket shape minimizes material packing in the crease of a rotor vane, making it optimal for sanitary or food grade valves.
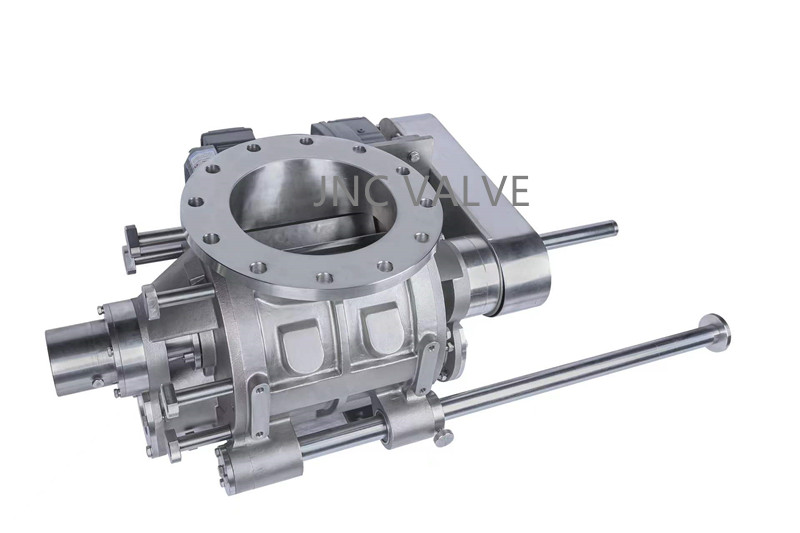
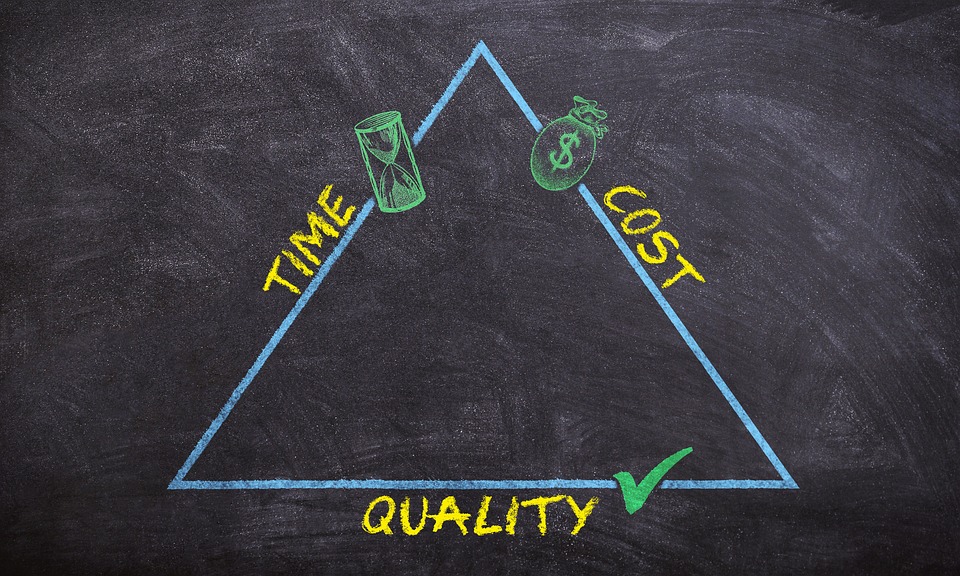
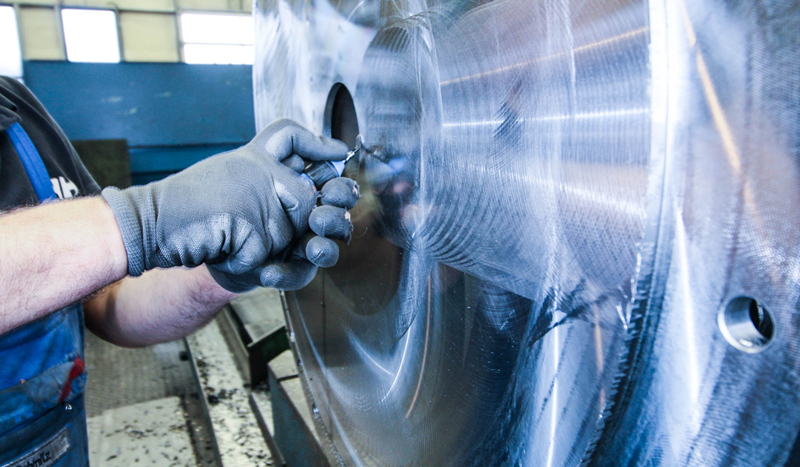
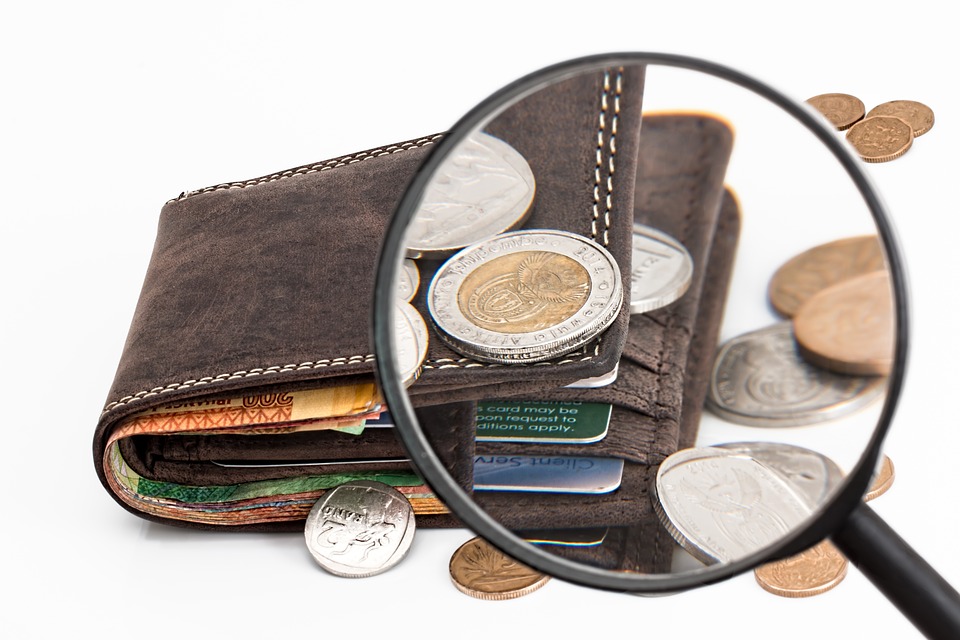
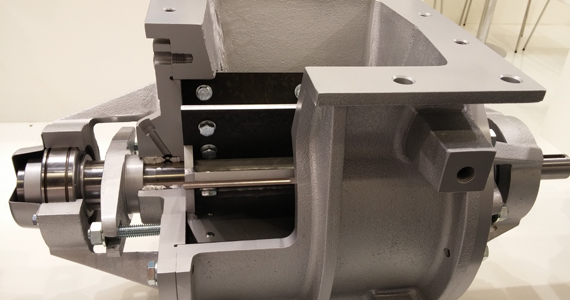
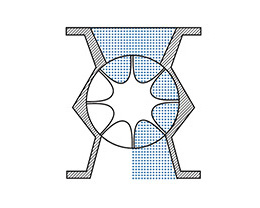